L'usinage CNC à 5 axes représente l'une des technologies les plus avancées et les plus efficaces dans le domaine de la fabrication de précision. Contrairement aux systèmes traditionnels à 3 axes, les machines à 5 axes peuvent déplacer les outils de coupe ou la pièce à usiner le long des axes de la machine. cinq axes différents simultanément. Ce mouvement élargi permet de créer des géométries complexes et des surfaces courbes en une seule fois, ce qui améliore considérablement la précision et la productivité.
Des turbines aérospatiales aux implants médicaux complexes, les industries qui exigent des pièces de haute performance s'appuient de plus en plus sur l'usinage 5 axes pour répondre à leurs exigences en matière de conception et de qualité. Dans cet article, nous allons explorer les principaux avantages, les capacités essentielles et les applications concrètes de l'usinage CNC 5 axes, afin d'aider les ingénieurs et les acheteurs à mieux comprendre sa valeur dans la fabrication moderne.
Qu'est-ce que l'usinage CNC 5 axes ?
L'usinage CNC 5 axes est un processus de fabrication soustractive dans lequel un outil de coupe se déplace le long de cinq axes - X, Y, Z - et de deux axes de rotation (A et B). Ce mouvement simultané permet de créer des pièces très complexes avec des géométries compliquées en un seul réglage, ce qui réduit la nécessité de procéder à de multiples fixations ou repositionnements.
Contrairement à l'usinage 3 axes, qui limite le parcours de l'outil à trois directions, les systèmes 5 axes offrent une plus grande liberté de mouvement. Ils sont donc idéaux pour les composants aérospatiaux, médicaux et automobiles qui nécessitent une grande précision et des tolérances serrées.
Logiciel de FAO et exigences de programmation
L'un des éléments essentiels de la réussite de l'usinage CNC à 5 axes est l'utilisation d'une technologie de pointe. CAM (fabrication assistée par ordinateur). Ces programmes traduisent les modèles CAO 3D en parcours d'outils précis qui commandent les mouvements multi-axes de la machine. Par rapport à la programmation 3 axes, la génération de parcours d'outils 5 axes est nettement plus complexe en raison de la rotation et de l'inclinaison continues de l'outil ou de la pièce à usiner.
Pour exploiter pleinement les capacités des machines à 5 axes, les fabricants s'appuient sur un logiciel de FAO qui prend en charge la détection des collisions, l'optimisation de l'orientation de l'outil et le contrôle dynamique des mouvements. Des programmes tels que HyperMill, Mastercam, Siemens NX et Fusion 360 sont couramment utilisés dans l'industrie.
Une bonne programmation permet non seulement de garantir la précision des pièces, mais aussi de minimiser l'usure des machines et d'améliorer l'efficacité de la production. Les programmeurs qualifiés doivent également comprendre les stratégies de fixation, la cinématique des axes et le post-traitement afin d'affiner les résultats pour des machines spécifiques.
Alors que l'usinage 5 axes continue d'évoluer, il est essentiel d'investir dans un logiciel de FAO performant et dans des programmeurs expérimentés pour obtenir des résultats optimaux.
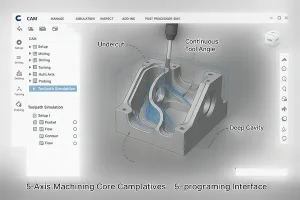
Interface logicielle FAO avancée utilisée pour la programmation CNC à 5 axes, y compris la détection des collisions et l'optimisation des trajectoires d'outils.
Avantages de l'usinage CNC 5 axes
L'un des principaux avantages de l'usinage CNC à 5 axes est sa capacité à produire des pièces complexes et de haute précision avec moins de réglages. En usinant sous plusieurs angles en une seule opération, les fabricants peuvent éliminer le besoin de repositionnement, ce qui permet non seulement de gagner du temps, mais aussi de réduire le risque d'erreur humaine.
En outre, les systèmes à 5 axes permettent d'obtenir de meilleurs états de surface en permettant à l'outil de coupe de conserver une orientation optimale par rapport à la pièce à usiner. Cela est particulièrement utile pour les applications qui nécessitent des contours lisses, comme les pales de turbines, les moules et les implants médicaux.
La réduction du temps de préparation et l'amélioration de la précision permettent également d'accroître l'efficacité et de réaliser des économies tant au niveau du prototypage que de la production à grande échelle.
Principales capacités de l'usinage CNC à 5 axes
L'usinage CNC à 5 axes offre un niveau de précision et de polyvalence inégalé par les systèmes conventionnels à 3 axes. L'une des capacités clés est la possibilité d'usiner des contre-dépouilles, des cavités profondes et des contours complexes sans avoir recours à des réglages multiples ou à un outillage spécialisé. Cela permet aux ingénieurs de concevoir des pièces aux géométries complexes qu'il serait autrement impossible ou irréalisable de produire.
Une autre capacité majeure est l'usinage 5 axes en continu, qui permet à l'outil de maintenir des angles de coupe optimaux tout au long du processus. Il en résulte des temps de cycle plus courts, une meilleure intégrité de la surface et une moindre usure de l'outil, ce qui est idéal pour les matériaux de grande valeur tels que le titane, l'Inconel et les aciers trempés.
Les machines 5 axes modernes sont également compatibles avec les logiciels de CAO/FAO avancés, ce qui permet aux fabricants de simuler et d'optimiser les parcours d'outils avant le début de la production. Cette intégration numérique améliore la cohérence, réduit le temps de programmation et permet un prototypage rapide ainsi que des productions en grande série.
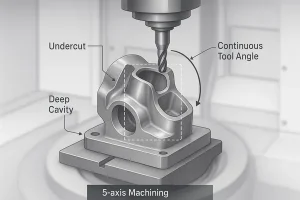
Visualisation des fonctions essentielles de l'usinage CNC à 5 axes, notamment le détalonnage, le fraisage de cavités profondes et l'ajustement continu de l'outil.
Les meilleurs matériaux pour l'usinage CNC 5 axes
Le potentiel de l'usinage CNC 5 axes est pleinement exploité lorsqu'il est associé à des matériaux qui bénéficient d'une précision multi-axes et d'un repositionnement minimal. Les métaux tels que titane, aluminiumet Inconel sont couramment utilisés en raison de leur résistance, de leur légèreté et de leur intégrité structurelle. Ces matériaux sont particulièrement répandus dans les applications aérospatiales et médicales où les performances mécaniques et la réduction du poids sont essentielles.
Par exemple, titane est biocompatible et résistant à la corrosion, ce qui le rend idéal pour les implants et les outils chirurgicaux. aluminium est largement utilisé pour les composants aéronautiques en raison de son excellente usinabilité et de son rapport résistance/poids. Inconelun alliage de nickel haute performance, est privilégié pour les pièces exposées à des températures et à des contraintes mécaniques extrêmes, telles que les pales de turbines.
En plus des métaux, plastiques de haute performance comme PEEK et Delrin sont également usinables avec des systèmes à 5 axes. Ces matériaux sont utilisés dans les boîtiers électroniques, les gabarits de précision et les composants nécessitant une résistance chimique ou une isolation.
Le choix du bon matériau est essentiel pour garantir la fabricabilité et les performances à long terme de la pièce. Avec la capacité de traiter une gamme aussi large, l'usinage CNC à 5 axes offre aux ingénieurs une flexibilité inégalée, tant dans le choix des matériaux que dans la qualité de la pièce finale.
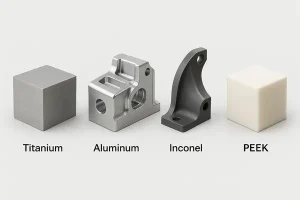
Matériaux courants utilisés dans l'usinage CNC à 5 axes pour les applications aérospatiales, médicales et industrielles.
Finition de surface et tolérances
L'un des principaux atouts de l'usinage CNC à 5 axes est sa capacité à obtenir des finitions de surface supérieures et des tolérances extrêmement serrées. Comme l'outil peut approcher la pièce sous des angles optimaux, il réduit le besoin de repositionnement et d'opérations secondaires, qui introduisent souvent des erreurs d'alignement ou des incohérences de surface.
Le mouvement de coupe continu et ininterrompu rendu possible par l'usinage 5 axes simultanés minimise également les marques d'outil et le broutage, produisant des surfaces plus lisses, même sur des contours complexes. Cette caractéristique est particulièrement précieuse dans des secteurs tels que l'aérospatiale et la médecine, où l'efficacité aérodynamique ou la biocompatibilité dépendent d'une qualité de surface précise.
En termes de tolérances, les machines à 5 axes peuvent couramment maintenir des tolérances de ±0,005 mm ou mieux, en fonction de la machine, de l'outillage et de la configuration. Ce niveau de précision est essentiel pour les composants qui nécessitent des ajustements de haute performance, tels que les pales de turbines, les implants orthopédiques ou les assemblages de boîtiers optiques.
Des finitions de haute qualité et des tolérances constantes réduisent la nécessité d'un post-traitement, ce qui permet de gagner du temps et de l'argent tout en améliorant l'intégrité du produit.
Applications de l'usinage CNC à 5 axes
La polyvalence de l'usinage CNC à 5 axes le rend indispensable dans de nombreuses industries où la précision, la complexité et la fiabilité sont essentielles.
Aérospatiale :
Dans l'aérospatiale, l'usinage 5 axes est utilisé pour fabriquer des aubes de turbine, des composants de moteur, des cadres structurels et des boîtiers qui nécessitent des rapports poids/résistance élevés et des profils aérodynamiques précis.
Dispositifs médicaux :
Les fabricants de produits médicaux font appel à l'usinage 5 axes pour produire des implants orthopédiques, des outils chirurgicaux et des composants dentaires avec formes complexesLes matériaux biocompatibles, les finitions de surface fines et les matériaux biocompatibles.
Automobile :
Les applications automobiles comprennent les prototypes de moteurs, les boîtiers de transmission, les pièces de suspension et l'outillage de moulage. La possibilité d'usiner toutes les faces d'une pièce en une seule fois améliore les délais d'exécution et garantit une précision dimensionnelle constante.
Secteur de l'énergie :
L'usinage 5 axes est également utilisé dans le secteur de l'énergie pour des pièces telles que les roues, les corps de pompe et les disques de turbine, des composants qui présentent souvent des surfaces incurvées et nécessitent des propriétés mécaniques exceptionnelles.
En prenant en charge divers matériaux et géométries, l'usinage CNC à 5 axes joue un rôle essentiel dans les industries où l'échec n'est pas envisageable.
Prêt à améliorer vos capacités de production ?
Que vous développiez des composants de qualité aérospatiale ou que vous recherchiez des tolérances plus serrées pour des pièces médicales ou automobiles, l'usinage CNC 5 axes offre la précision et la flexibilité que votre projet exige. Chez Minghe CNC, nos machines 5 axes de pointe et notre équipe d'ingénieurs experts sont prêts à répondre à vos besoins les plus exigeants.
Contactez-nous dès aujourd'hui pour discuter de vos besoins en matière d'usinage CNC personnalisé ou demander un devis gratuit.
Vous recherchez une vue d'ensemble structurée des principes de l'usinage à 5 axes, des types de machines et des conseils de conception ?
Consultez notre brochure complète Guide d'usinage CNC à 5 axes pour en savoir plus.