유럽 애플리케이션을 위한 CNC 가공 정밀도와 효율성을 개선하고 싶으신가요? 항공우주, 자동차 또는 중장비 고객을 대상으로 하든, 높은 정확도, 엄격한 공차 및 사이클 시간 단축을 요구하는 제조업체를 위한 실행 가능한 전략이 마련되어 있습니다.
Minghe CNC는 실무 작업장 경험과 국제적인 CNC 가공 모범 사례를 결합하여 일관된 고품질 부품을 대규모로 제공할 수 있도록 지원합니다.
1. 머신 설정 및 유지보수 최적화
스핀들과 축을 정기적으로 보정하고 칩과 윤활 시스템을 청소하면 CNC 작업에서 일관된 위치 정확도를 유지할 수 있습니다. 📉
예시: 한 고객은 4%에서 다음과 같이 스크랩을 줄였습니다. 1.2%처리량을 최대 18%까지 개선했습니다.
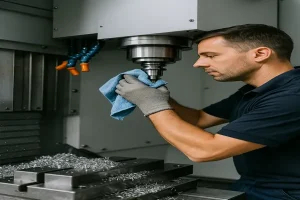
생산 정밀도를 보장하기 위한 일상적인 CNC 기계 보정 및 청소.
2. 스핀들 속도 및 이송 속도 균형 맞추기
특정 재료와 툴링에 맞게 RPM과 이송 속도를 조정합니다. 예를 들어, 알루미늄에 AlTiN 코팅된 엔드밀은 다음 주변에서 가장 잘 작동합니다. 1800 RPM 및 0.08-0.12 mm/rev를 사용하여 사이클 시간을 최대 12%까지 단축하고 마감 품질을 개선했습니다. 📈
결과: 표면 거칠기가 다음에서 개선되었습니다. Ra 1.2 ~ 0.9 공구 수명 증가 ~15%
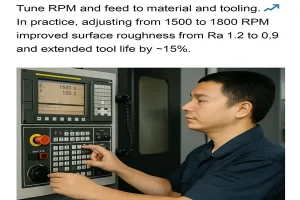
CNC 가공 성능을 최적화하려면 스핀들 속도와 이송 속도의 균형을 맞추는 것이 중요합니다.
.
3. 스마트 툴링 및 도구 경로 전략 사용
코팅된 카바이드 공구를 사용하고 황삭(~80% 재료 제거)과 정삭 패스(~0.1mm)를 결합합니다. CAM 소프트웨어에서 경로를 시뮬레이션하여 충돌을 방지하고 가공 시간을 단축합니다.
결과: 사이클 시간이 다음에서 감소했습니다. 15:23~13:33-최적화된 G-코드로 12% 개선.
4. 설정 최소화(OP)
위치를 변경할 때마다 비절삭 시간이 추가됩니다. 더 나은 부품 설계 또는 다축 가공을 사용하여 설정을 4개에서 2개로 줄이면 전체 사이클 시간을 다음과 같이 단축할 수 있습니다. ~20%.
5. 실시간 공구 마모 모니터링
기계 내 프로브 또는 음향 센서를 사용하여 생산 중 공구 마모를 추적하세요. 조기에 감지하면 결함 및 예기치 않은 가동 중단을 방지하여 자재와 노동력을 절약할 수 있습니다.
6. 가상 머시닝 시뮬레이션 사용
전체 작업을 가상으로 시뮬레이션하여 실제 절단 전에 지원되지 않는 피처, 비효율적인 경로 또는 충돌 위험을 감지할 수 있습니다. 연구 결과에 따르면 시뮬레이션은 다음과 같은 방식으로 재작업률을 줄여줍니다. 30-60%.
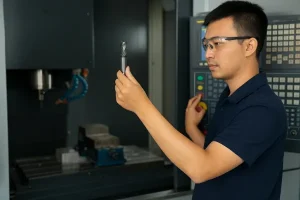
스마트 공구 경로 전략은 CNC 가공에서 사이클 시간을 단축하고 충돌을 방지합니다.
7. 매장 레이아웃 및 운영자 교육 최적화
기계를 논리적으로 배치하여 불필요한 보행이나 취급을 줄이십시오. 15-25%. SOP 및 다음과 같은 고급 기술에 대한 정기적인 교육을 제공합니다. 트로코이드 밀링다음과 같이 효율성이 향상되었습니다. 58% 까지 저장하고 35만유로/년 항공우주 애플리케이션에 사용됩니다.
이러한 전략은 유럽 제조업체의 CNC 가공에서 치수 정확도 향상, 사이클 시간 단축, 비용 효율적 생산 등 측정 가능한 결과를 제공하는 것으로 입증되었습니다. 이러한 전략을 적용하여 정밀 제조 분야에서 전략적 우위를 확보하세요.