CNC machining, short for Computer Numerical Control machining, is a manufacturing process that uses computerized controls and precision cutting tools to remove material from a solid workpiece. The process transforms digital designs into physical parts by automating tool movements along multiple axes—typically X, Y, and Z—based on pre-programmed instructions.
How Does CNC Machining Work
1. Digital Design and Programming
The CNC process begins with a digital blueprint. An engineer first creates a 3D model of the part using CAD (Computer-Aided Design) software. This digital design is then imported into CAM (Computer-Aided Manufacturing) software, which translates it into machine-readable G-code. This G-code contains all the instructions needed to guide the machine’s movements, tool paths, speeds, and cutting depths.
2. Machine Setup
Before machining begins, an operator secures the selected raw material—often a block of metal or plastic—onto the CNC machine’s worktable. At the same time, the necessary cutting tools are loaded into the spindle, ensuring the machine is ready to execute the G-code instructions.
3. Machining Operation
Once the program is loaded, the CNC machine operates autonomously. The spindle rotates the cutting tool at high speed, precisely removing material layer by layer as it follows the G-code’s programmed path. Depending on the part’s complexity, the machine may automatically change tools or use multi-axis movements to reach all necessary surfaces and geometries.
4. Quality Control and Final Product
Throughout the entire process, a closed-loop control system monitors the operation. Sensors continuously provide feedback to ensure the tool’s position and cutting accuracy align perfectly with the programmed instructions. The final result is a highly precise finished component that matches the original digital design.
Key Benefits of CNC Machining
CNC machining offers a wide range of benefits that make it a go-to solution for modern manufacturing.
Precision and Accuracy
CNC machines can achieve extremely tight tolerances—often within ±0.01 mm—making them ideal for components that demand exact specifications. This high accuracy ensures consistent quality across large production runs.
Flexibility
CNC machines can handle a wide variety of materials, including aluminum, stainless steel, brass, titanium, and various plastics. They are capable of producing both simple and complex parts, from basic brackets to intricate aerospace components, all without the need for custom tooling.
Speed and Repeatability
Once a program is created, CNC machines can produce identical parts rapidly and with minimal variation, reducing human error and labor costs.
Ease of Modification and Scalability
The digital nature of CNC allows for easy modifications, quick prototyping, and seamless scalability from one-off pieces to full-scale production.
Together, these benefits make CNC machining an efficient, cost-effective, and reliable choice for manufacturers seeking high-quality parts with minimal lead time.
Main CNC Processes
The core of CNC machining lies in the flexible application of various cutting processes, each matched to a specific type of machine to complete different manufacturing tasks.
Milling
This is one of the most common CNC processes. It uses a rotating cutting tool to remove material from a stationary workpiece, creating flat surfaces, slots, holes, and complex 3D contours. CNC milling machines (such as 3-axis or 5-axis mills) are the equipment used to perform this process.
Turning
Unlike milling, turning involves a stationary cutting tool moving along the surface of a workpiece that is rotating at high speed. This process is specifically used to produce parts with perfect cylindrical, conical, or threaded features. CNC lathes (or turning centers) are the tools that carry out this process.
Drilling
As the name suggests, this is the process of making precise holes in a workpiece. CNC drilling machines can automatically perform drilling, reaming, tapping, and other operations, ensuring the accuracy of hole positions and depths.
Electrical Discharge Machining (EDM)
This unique process uses electrical sparks to erode conductive materials. It is particularly effective for machining extremely hard metals that are difficult to cut with conventional tools or for creating intricate internal geometries.
Understanding how these processes work with different types of CNC machines is key to grasping the fundamentals of modern precision manufacturing. Together, they form the powerful capabilities of CNC machining, transforming digital designs into highly precise physical products in the real world.
Types of CNC Machines
CNC machining encompasses a variety of machine types, each tailored for specific manufacturing tasks. Understanding the main categories can help engineers and buyers select the right equipment for their needs.
Classification by Type
Based on their primary function and machining process, CNC machines can be divided into the following categories:
CNC Milling Machines
These machines use a high-speed rotating tool to remove material from a stationary workpiece. They are ideal for creating flat surfaces, grooves, holes, and complex 3D contours.
CNC Lathes (Turning Centers)
Unlike mills, lathes work by rotating the workpiece at high speed while a stationary tool moves along its surface to remove material. This type of machine is the top choice for manufacturing all kinds of cylindrical parts, such as shafts, bushings, and threaded components, and is known for its exceptional symmetry and surface finish.
CNC Drilling Machines
These machines are specifically designed to create precise holes. A CNC drilling machine can complete a variety of operations in a single setup, including drilling, tapping, and reaming, ensuring extreme accuracy of hole positions and depths.
CNC Routers
Routers are primarily used for machining softer materials like plastics, wood, and composites. They are known for their speed and efficiency and are commonly used in sign making, furniture, and prototyping.
CNC Electrical Discharge Machining (EDM) Machines
This is a non-traditional machining method that uses electrical sparks to erode conductive materials. EDM machines are particularly effective for working with extremely hard metals or for creating complex internal shapes that are difficult to produce with conventional tools.
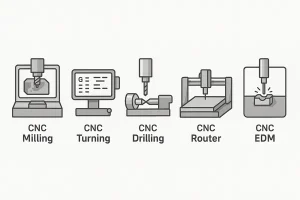
Key types of CNC machines such as milling, turning, drilling, and EDM.
Understanding Machine Capability: Classification by Axes
Beyond classifying machines by type, CNC machines are also often categorized by the number of motion axes they can control simultaneously. This directly determines the complexity and efficiency of the parts they can machine.
3-Axis Machines
This is the most basic type, able to move along the X, Y, and Z Cartesian axes. It’s suitable for machining flat surfaces, 2D contours, and simple 3D shapes.
4-Axis Machines
These add a rotary axis (usually A or B) to the 3-axis setup. This allows the machine to process the sides of a part without re-fixturing, making them ideal for complex asymmetrical parts.
5-Axis Machines
With two rotary axes (usually A and C, or B and C), the cutting tool can approach the workpiece from almost any angle. This enables all machining to be completed in a single setup, greatly improving efficiency and precision. They are essential for manufacturing complex parts like aerospace blades and medical devices.
This classification system allows buyers and engineers to more precisely select the right equipment for their project’s complexity and budget.
Common Materials Used in CNC Machining
One of the key strengths of CNC machining lies in its wide material compatibility. From lightweight metals to high-performance polymers, CNC machines can handle a diverse range of materials to suit various engineering and functional needs.
Metals
Metals are widely used in CNC machining due to their excellent strength, durability, and thermal conductivity.
-
Aluminum
Highly machinable, lightweight, and corrosion-resistant. Commonly used in aerospace, automotive, and electronics applications.
-
Stainless Steel
Offers excellent strength, wear resistance, and corrosion resistance, making it suitable for medical devices and structural components.
-
Brass
Known for its smooth finish and low friction, brass is often used for valves, fittings, and decorative parts.
-
Titanium
Strong, lightweight, and biocompatible, titanium is favored in aerospace and medical industries despite its higher machining difficulty.
Plastics
Plastics are widely used in CNC machining for various functional and prototype parts due to their lightweight, corrosion resistance, electrical insulation, and economic advantages.
-
ABS
Lightweight and impact-resistant, ideal for enclosures and housings.
-
Nylon
Offers good wear resistance and flexibility, often used in gears and bushings.
-
POM (Delrin)
Has excellent dimensional stability and low friction, widely used in mechanical components.
-
PEEK
A high-performance thermoplastic with excellent thermal and chemical resistance, used in aerospace and medical parts.
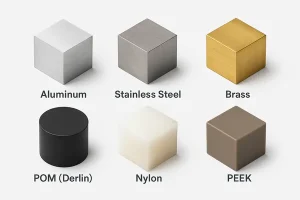
Overview of common materials used in CNC machining—both metals and plastics.
Composites, Foams, and Wood
Beyond metals and plastics, CNC machining is also widely used for the following materials to meet the specific demands of certain industries and applications:
-
Composites: Materials such as carbon fiber and fiberglass. They offer an extremely high strength-to-weight ratio, making them an ideal choice for aerospace and high-performance sports equipment.
-
Foams: Including polyurethane and structural foams. They are lightweight and easy to machine, commonly used for rapid prototyping, model making, and casting molds.
-
Wood: From hardwoods to plywood, CNC routers can quickly and precisely cut and engrave wood, which is widely applied in furniture manufacturing, artwork, and architectural models.
The choice of material depends on factors such as mechanical properties, environmental conditions, tolerance requirements, and cost. CNC machining’s ability to work with such a broad material spectrum makes it suitable for both prototype and production-stage components across industries.
Applications in Modern Industry
CNC machining plays a vital role across a wide range of industries due to its precision, versatility, and scalability. From highly regulated sectors to general manufacturing, CNC technology supports both prototyping and full-scale production of critical components.
Aerospace
Aircraft parts require exceptional accuracy and material performance. CNC machining is used to produce structural brackets, turbine components, housings, and even lightweight aluminum airframe parts with tight tolerances and high surface quality.
Automotive
CNC machining supports both prototyping and production of engine parts, transmission housings, suspension components, and dashboard structures. Its ability to work with metals like aluminum and stainless steel ensures durability and performance.
Medical Devices
With strict safety and precision standards, the medical industry relies on CNC machining for surgical instruments, orthopedic implants, dental components, and diagnostic equipment parts—often made from biocompatible materials such as titanium or PEEK.
Electronics
CNC machines fabricate enclosures, connectors, and heat sinks from aluminum or plastic, ensuring exact fits and optimal thermal performance in compact electronic devices.
Industrial Equipment
From custom gears to machine frames and robotic arms, CNC machining produces durable, reliable components that withstand repetitive motion and stress in manufacturing environments.
These applications demonstrate CNC machining’s adaptability to both complex and high-volume part requirements, making it a cornerstone of modern industrial production.
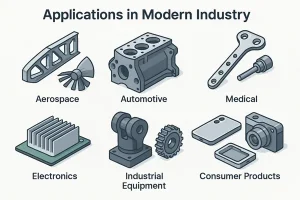
Visual summary of typical CNC-machined parts used in modern industries such as aerospace, automotive, and medical.
CNC Machining vs Traditional Machining
Understanding the difference between CNC machining and traditional manual machining is essential for making the right manufacturing decisions. While both methods shape materials into functional parts, their core difference lies in their level of automation and control.
Traditional machining relies entirely on a skilled operator who manually guides cutting tools and controls every movement of the machine. This is a hands-on, physically demanding process that depends on the operator’s experience and dexterity. As a result, it can be prone to human error and is less consistent across multiple parts.
In contrast, CNC machining is a fully automated process. Once the digital design is programmed, the computer takes over. It precisely controls the machine’s movements, tool paths, and speeds without human intervention. This automation ensures a level of precision, repeatability, and efficiency that is simply unachievable with manual methods.
Key Differences at a Glance
Feature | CNC Machining | Traditional Machining |
Control | Computer-controlled | Manual, human-controlled |
Precision | Very high, consistent | Varies with operator skill |
Speed | Fast, especially for complex parts | Slower, labor-intensive |
Complexity | Excellent for intricate geometries | Limited to simpler shapes |
Repeatability | High, identical parts | Low, prone to variation |
Labor | Less labor-intensive, requires programming skills | Highly labor-intensive, requires manual skill |
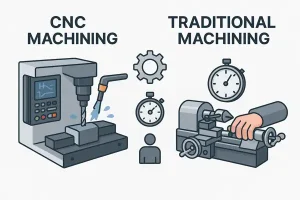
A side-by-side visual comparison of CNC machining and manual machining processes.
Is CNC Machining a Good Career?
For those who are interested in manufacturing, technology, and hands-on work, CNC machining is an excellent career choice. It combines traditional craftsmanship with modern automation, offering a stable and promising career path.
One of the biggest advantages of this field is its high demand and stability. As manufacturing continues to digitize, CNC operators and programmers are highly sought after across a variety of industries, including aerospace, medical, automotive, and electronics. This ensures a consistent job market for the profession.
Of course, the career requires a set of key skills, including understanding design blueprints, operating software, troubleshooting technical issues, and having a deep knowledge of materials and cutting tools. As technology advances, a willingness to continuously learn new software and machine operations is crucial for success.
From a salary perspective, CNC operators are often competitively compensated, and as they gain experience and skills, they have the opportunity to advance to higher-paying positions such as CNC programmer, quality control manager, or even shop supervisor, which provides a clear path
Career Outlook for CNC Machinists
Many people have questions about the career path for CNC machinists, focusing on job demand, salary, and job demands.
Job Demand
The demand for CNC machinists is strong. According to the U.S. Bureau of Labor Statistics (BLS), employment in the field is projected to grow by 2% through 2032, adding over 365,000 jobs. Despite this modest growth rate, a significant skills gap exists due to a large number of experienced machinists nearing retirement. This creates consistent job opportunities, especially in high-precision manufacturing sectors like aerospace and medical devices, making it a stable career choice.
Salary and Earning Potential
You can earn a good living as a CNC machinist. According to BLS data from May 2024, the median annual salary for CNC machine operators is approximately $52,900, while experienced CNC programmers earn a median of $69,880. Top-level programmers can even earn over $99,000 annually. This data shows that a significant earning potential exists as you gain experience and skills.
Technical Demands and Required Skills
CNC is a demanding job, but its challenges are more technical than physical. It places very high demands on practitioners, which are reflected in the following aspects:
-
Technical Complexity: Job descriptions on recruiting websites often require candidates to have skills such as proficiency in CAD/CAM software to translate designs into machine programs and the ability to write and edit G-code and M-code.
-
High-Precision Requirements: In fields like aerospace and medical, part tolerances can be as small as a few microns. This demands extreme focus and attention to detail from machinists, as any small error can lead to costly material waste.
-
Problem-Solving Ability: When a machine malfunctions or the machining process is not meeting expectations, machinists must be able to quickly diagnose and troubleshoot issues.
These specific skill requirements commonly found in job postings directly demonstrate the professional and high-entry-level nature of the work. This is also why experienced CNC professionals are highly valued and better compensated by the market.
How to Reduce CNC Machining Costs
The cost of CNC machining is not fixed; it is largely determined by a part’s design and manufacturing strategy. By considering manufacturability during the design phase, you can significantly save both time and money.
Simplify Design and Tolerances
Design complexity is a major cost driver. Overly complex geometries, deep and narrow pockets, and very small internal radii require smaller tools and longer machining times. Additionally, specifying tight tolerances only in functionally critical areas will help you avoid unnecessary machining and quality control costs.
Choose Cost-Effective Materials
Material cost is a significant part of the total price. Using materials that are easy to machine and lower in cost, such as Aluminum 6061 or Brass, is much cheaper than using high-strength alloys like Titanium or Stainless Steel. When starting a design, it is crucial to select the most economical material based on the part’s actual performance requirements.
Consider Batch Size
The initial setup costs for CNC machining (including programming and fixturing) are fixed. This means that the larger the batch size, the lower the cost per part will be. If possible, consolidate multiple prototype designs into a single order or increase the order quantity to get a better price.
Avoid Unnecessary Surface Finishes
Many surface finishing processes, such as anodizing, polishing, or heat treating, add extra cost and lead time. Only specify these finishes when they are truly required for the part’s function or appearance.
Reduce Setups
Each time a part is re-fixtured, it adds to the setup time and the risk of error. By optimizing the design to allow the part to be completed in the fewest possible setups, you can significantly increase efficiency and lower costs.
By adopting these strategies during the design and planning phases, you can work more effectively with your CNC machining partner to maximize cost control without sacrificing quality.
Frequently Asked Questions
Why is CNC machining so expensive?
The high cost of CNC machining primarily stems from the expensive equipment, software, and programming time, as well as material costs. Although the initial investment is high, its precision and efficiency often lead to long-term cost savings.
How do I learn CNC machining?
Learning CNC machining typically requires a combination of theory and practice. You can begin with courses at a vocational or technical school, and then gain hands-on experience through online tutorials and working in a real workshop.
What is the difference between CNC machining and 3D printing?
CNC machining is a “subtractive” manufacturing process that shapes parts by removing material through cutting. In contrast, 3D printing is an “additive” manufacturing process that builds parts layer by layer. They differ fundamentally in their manufacturing principles, materials, and applications.
Conclusion
CNC machining continues to transform modern manufacturing by offering exceptional accuracy, material versatility, and design flexibility. From one-off prototypes to high-volume production, it enables engineers and buyers to turn digital concepts into functional parts with speed and precision.
Understanding the fundamentals of CNC machining—and how to choose the right partner—empowers you to streamline production, reduce costs, and improve product quality.
Looking for a reliable CNC machining partner? Contact us today to get a quote and expert support.